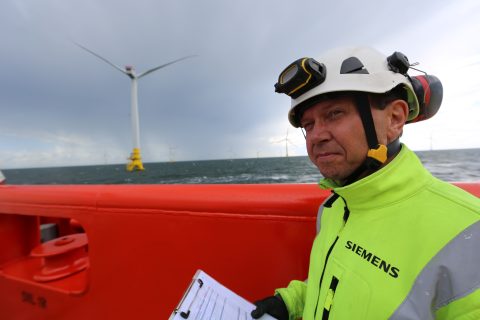
Article courtesy Siemens TheEnergyBlog
2015 marked the beginning of a new era in offshore wind power, when Siemens Wind Power Service christened the first of two purpose-built Service Operation Vessels (SOVs). Now one year on we take a look back at the 1st year to find out how the vessel has performed and how those who use them every day feel they have improved their working lives at sea. In this article we follow up with Andreas Geißen, who is one of the Environmental Health & Safety Officers responsible for ensuring the day-to-day safety of the teams who service the wind farm from this pioneering and floating offshore base.
Andreas, what are the SOV’s most important safety features as far as you’re concerned?

With the on-board hospital we have the necessary facilities and equipment to deal with most normal medical situations that could arise on a daily basis.
The SOV is state of the art and conforms to all the highest safety standards and we have everything we need on board to respond to any emergencies. But for me, the two most important features would be the vessel’s on-board hospital and the Ampelmann walk-to-work gangway system. These are the two main features of the SOV that really strengthen our commitment to Zero Harm. The hospital for obvious reasons – a sick bay means we have the necessary facilities and equipment to deal with most normal medical situations that could arise on a daily basis. And the hydraulic gangway system: because it’s central to the whole SOV safety concept itself.
Thankfully in the first year of operations we have only had a few very minor incidents. So we’re very happy and proud to report nothing more than a few finger cuts and splinters.
You mentioned the gangway system, how does it contribute towards safety?

In terms of safety the Ampelmann gangway system is a tried and tested almost risk-free solution.
The biggest risks associated with offshore wind service are when the technicians transfer to and from the wind turbines. And with traditional CTV (Crew Transfer Vessel) transfers there are many factors that can go wrong. The service technician has to step off a moving boat onto the ladder of the wind turbine so everything from the unpredictability of weather conditions, wave heights or a failure in safety equipment could potentially pose a risk.
By comparison, the Ampelmann gangway system is a tried and tested almost risk-free solution. It can be used in almost any weather conditions in the Baltic Sea in wave heights of up to 2.5 m. It’s a hydraulic system, which counterbalances the effect of the waves, so it presents technicians with a very steady and stable platform from which they can just walk to and from work. In the course of this year, we’ve made over 7,400 technician transfers in this way without any incidents.
Do you still transfer technicians by boat as well?
Sure, it’s integral to our flexible SOV service concept. We have a very good Safe Transfer Boat (STB 12) on-board. But we only allow technicians to transfer to the turbines from this when wave heights are below 1.5 m. So between the boat and the gangway we have the best of both worlds. We have the means to safely transfer our techs to the turbines pretty much all year round in terms of the local sea conditions.
What have you learned during the first year here? How has this had an impact on safety?

Siemens has a very high commitment to an injury free workplace and our service team have a very high level of education and training to help achieve this.
You never stop learning when it comes to safety. Every day you meet a new situation. But we operate in an environment of continuous improvement. Our techs come back and identify new issues, which we discuss every evening in our Toolbox Meetings. We have a system now where everyone takes pictures of the things they see that could pose a potential risk. This makes it easier to discuss and find solutions. Any issues that we discover are then fed into our Siemens-wide centralised safety alert system. By the same token, we monitor all alerts coming back from the system to optimise what we do. It’s all about sharing best practices.
How important is training when it comes to safety in an offshore environment like this?
It’s incredibly important. Because we’re Siemens, our service team already has a very high level of education and training – but again, we’re always looking to improve. Now our established team is in place, we’re planning several drills for later in the year. These will involve putting our emergency turbine extraction plans to the test using the Ampelmann gangway. We plan to practice extractions from the base, the transfer platform and the ladder inside the turbine.
The SOV concept is quite different from more traditional CTV service concepts because your teams live as well as work from the vessel for several weeks at a time instead of sailing out each day. How does this impact in terms of health and safety?
I think it has very positive effects in terms of the wellbeing of our teams. Compared to CTV service operations, our technicians do not have to sail to and from work each day because we’re already based in the wind farm. This can help relieve the effects of things like fatigue and even seasickness.
The trip to a turbine may only take a relatively short time from shore, but with a CTV you can be waiting next to a turbine for the right transfer conditions for several hours when the sea is rough. During this time it’s fairly common for technicians to become seasick. I see many seasickness reports from other offshore wind farms via our centralised reporting system each month. By contrast, the only issues we have had with seasickness here have been a result of rough weather CTV transfers to and from Rostock for shift changes. As a result, we now move the SOV closer to shore when the weather’s bad to reduce the transfer time to shore for our people.
What has impressed you most about your first year aboard the SOV?
The engagement of all technicians when it comes to safety has been fantastic. I think that’s also down to the fact that we live as well as work together here. You get to know people in a different way as a result and everyone seems more open. I’ve noticed not just how the more experienced guys support the younger ones, but how the younger ones also actively ask questions. We have a great team here and I think there’s a very special bond in the way everyone looks out for each other.